Approach
- Mapping of the “As-Is” business processes at level 1-3, via multi-disciplinary workshops (for maximal embedding) with relevant teams and stakeholder, interviews and go-sees.
- Determination of the “To-Be” business processes at level 1-3, starting from customer needs and customer journeys, and using the bottlenecks and improvement opportunities from the As-Is workshops.
- Workshops’ output received by using SIPOC’s and Makigami’s. This includes process swim lanes, role determination, systems used, and determination of bottlenecks and improvement opportunities.
- Analysing improvement opportunities and mapping them via a “benefit-effort” methodology into a prioritised set of actions and projects.
- Piloting implementation of a to-be Order-to-cash process, using continuous improvement methodologies like performance cascading and daily management systems, for optimal organisational embedding.
- Further implementation of other processes via “oil-stain” thinking.
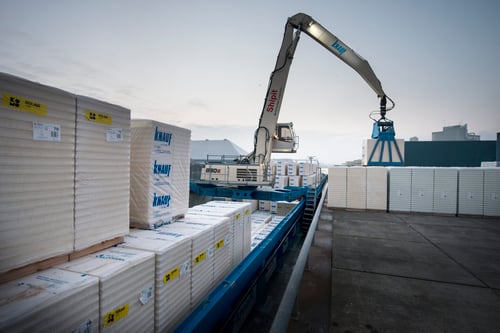
Results
- Process Maps defined at level 1-3 for the Core, Steering, and Supporting Processes.
- An adjusted and improved Process Map at level 1 (domain level) established to enhance the process thinking cross departments.
- A set of improvement projects and actions defined including prioritisation, based on the gaps identified. Larger improvement projects in start-up phase. Smaller improvement actions part of the daily management system installed.
- A daily management system in place based on a performance cascade for Order-to-Cash, with the intention to monitor performance and to get issues on the table, and to improve the cross organisational cooperation and understanding of each other needs. Set-up in continuous improvement style to ensure embedding and future ongoing improvements. Möbius is coach of this process and performs 2nd coaching so Knauf can take the lead in the future.
- Next steps is a role out of this methodology over all core processes to support Knauf in their strive for excellence.
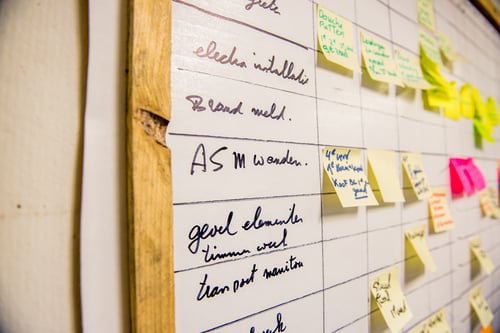